Šiuolaikinės ekonomikos dinamiškai besivystančių procesų sąlygomis, kuriant vis sudėtingesnes gamybos ir kontrolės procedūras, vienas aktualiausių jų tobulinimo būdų yra įvairių nuostolių optimizavimo metodų įdiegimas. Visų pirma, tai liečia įmonių išteklius - laikinuosius, finansinius, technologinius, energetikos ir kitus.
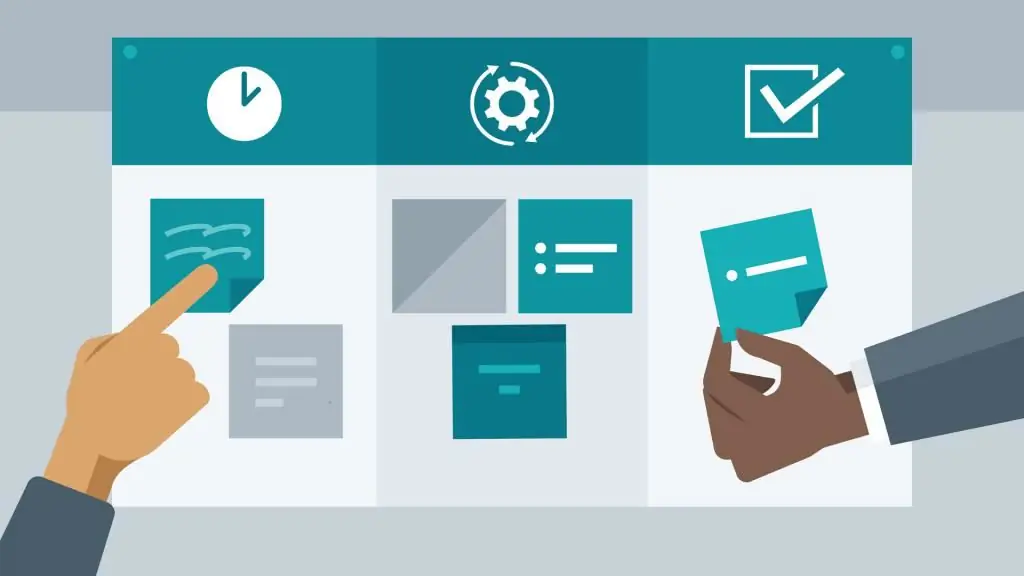
Veiklos ypatybės
Praktikoje yra tam tikros lubos, kurios siejamos su sistemos (organizacijos, įmonės) technologinio ir organizacinio išsivystymo lygiu. Akivaizdu, kad reikalauti visiško gamybos automatizavimo iš nedidelio siuvimo cecho pagal įvairius, o svarbiausia, ekonominius, kriterijus, nedera. Tačiau, nepaisant sistemos dydžio, būtina užtikrinti maksimalų ir optimalų turimų išteklių panaudojimą su minimaliais nuostoliais, kas galioja bet kuriai organizacijai ir veiklai.
Tokiu atveju tampa būtina naudoti progresyvius procesų valdymo metodus, kurie yra pagrįsti liesos arba „liesos“gamybos kūrimo teorija. Tai apima 5S ir TPM sistemas, vertės srauto sudarymą ir SMED ir kt.
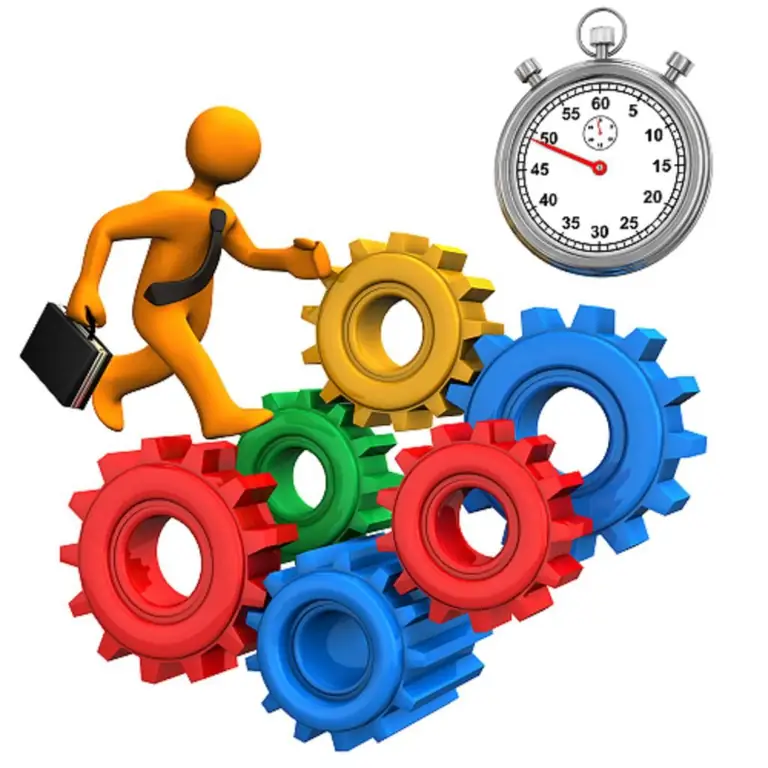
Inovacijų tikslas
Lean („liesa“) gamyba - tai specialių požiūrių į veiklos organizavimą sistema, kurios pagrindiniu tikslu laiko įvairių sistemos nuostolių pašalinimą. Mechanizmas gana paprastas: viskas, kas nesukuria klientui pridėtinės vertės, turi būti priskirta prie perteklinių (atliekų) ir pašalinta iš sistemos. Akivaizdu, kad „nuostolių“sąvoka yra kertinis akmuo, nes jų apibrėžimas tiesiogiai paveiks metodo veiksmingumą. Šiuo atveju išmokti susidėlioti savo specialistų vertės srautą yra didelis pranašumas paslaugų teikimo rinkoje
Nuostolių tipai
„Labi gamyba“yra viena iš pagrindinių gamybos logistikos sąvokų. Ir nors yra keli skirtingi nuostolių nustatymo būdai, išskirsime universaliausius tipus:
- Laukimo laikas - bet kokios veiklos prastovos sumažina galutinio produkto vertę. Laukimas medžiagų, įrangos remonto, informacijos ar nurodymų iš vadovybės sulėtina procesą ir padidina jo įgyvendinimo išlaidas.
- Nereikalingos operacijos (nereikalingas gaminių apdorojimas) - nereikalingos technologinės operacijos, projekto etapai, viskas, kaspateikiamos standartinėmis procedūromis, bet gali būti išlygintos neprarandant klientų pasitikėjimo.
- Nereikalingi darbuotojų judėjimai - įrankių, įrangos paieška, neracionalūs judesiai dėl prasto darbo vietos organizavimo ir pan.
- Nereikalingas medžiagų judėjimas - prastas inventorizavimo sistemos organizavimas, progresyvios transporto logistikos ir logistikos užsakomųjų paslaugų mechanizmų trūkumas.
- Atsargų perteklius - organizacijos apyvartinio kapitalo susiejimas dėl didelių išlaidų perteklinėms atsargų prekėms.
- Technologinės atliekos - pasenusios duomenų apdorojimo sistemos, technologiniai procesai ir apdorojimo būdai.
- Perprodukcijos nuostoliai - perteklinio produktų kiekio pagaminimas, dėl kurio padidėja jų sandėliavimo, transportavimo ir vėlesnio pardavimo sąnaudos.
- Intelektualiniai nuostoliai - darbuotojų ir darbuotojų iniciatyvumą skatinančių mechanizmų trūkumas, silpna racionalizavimo pasiūlymų sistema, kūrybiško požiūrio į darbą slopinimas.
Vienas iš labiausiai paplitusių metodų, padedančių pašalinti sistemos atliekas ir supaprastinti projekto vykdymą, yra vertės srauto sudarymas. Lean gamyba tuo pačiu leidžia sukurti prisitaikančią sistemą, kuri lanksčiai reaguoja į aplinkos pokyčius.
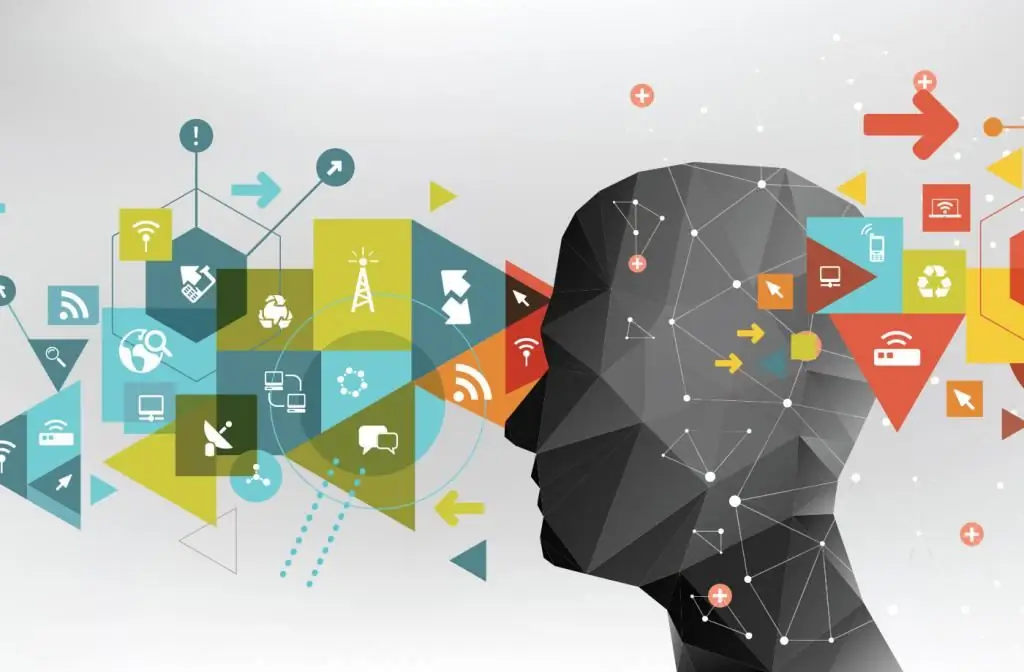
Vertės srautas
Vertės srautas yra visų veiksmų (operacijų), kurie atliekami su produktu, siekiant pasiektireikiamą būseną arba gauti reikiamas charakteristikas. Veiksmai skirstomi į dvi grupes:
- produkto vertės kūrimas (vertės pridėjimas);
- neprideda produktui vertės.
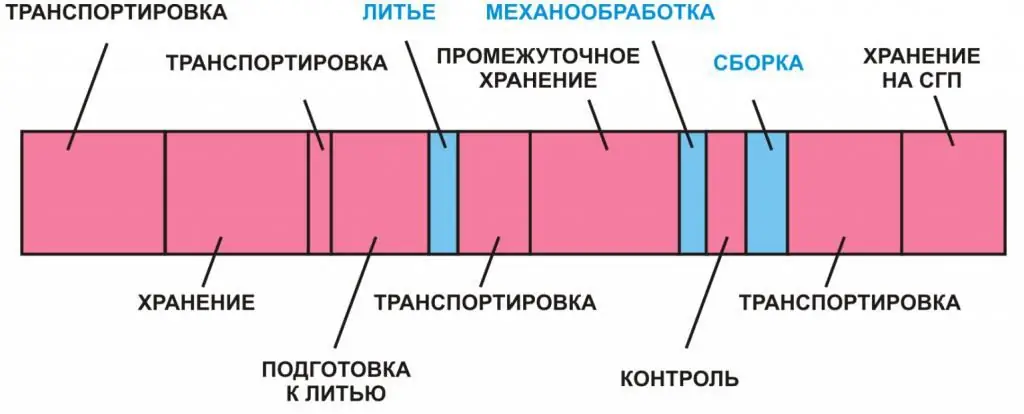
Kaip matyti iš pateikto paveikslo, gaminio technologinio keitimo etapai (mėlyna spalva) suteikia gaminiui pridėtinę vertę, o pagalbinių operacijų etapai - paruošimas, transportavimas, sandėliavimas - (rožinė spalva) - priešingai, verčiau sumažinkite prekės vertę dėl nereikalingų laiko nuostolių.
Atvaizdavimo procesas
Mapping technikos pagrindas - specialaus grafinio algoritmo sukūrimas, kuris laiku parodo produktų kūrimo procesą (projekto įgyvendinimą). Šis algoritmas vadinamas verčių srauto žemėlapiu, kuris yra grafinis modelis, pagrįstas konkrečiu simbolių (ženklų, simbolių) rinkiniu.
Pagrindiniai kortelės privalumai:
- vykdomo proceso grafinio modelio gavimas, atsižvelgiant į įvairius papildomus procesus holistiniam vizualiniam suvokimui (užduotis matyti bendrą įvykių tėkmę);
- galimybė aptikti įvairių tipų nuostolius visuose projekto etapuose;
- gaunamo modelio parametrinio optimizavimo galimybė, siekiant sumažinti visų rūšių išlaidas;
- dirbkite su įvairiais algoritmo rodikliais, kurie atsispindės realių procesų tobulėjime.
Vertės srauto atvaizdavimo formavimas remiantis standartiniais grafikais irsimboliai - stačiakampiai ir trikampiai kaladėlės, kryptinės ir laiptuotos rodyklės bei kitos figūros. Tai suteikia galimybę visiems specialistams viena kalba įrašyti tiriamo proceso etapus. Tuo pačiu rekomenduojama atskirti simbolius, atsižvelgiant į svarstomą srautą - materialų ar informacinį.
Lean Value Stream Mapping leidžia nustatyti visas vietas, kuriose kaupiasi nereikalingi elementai.
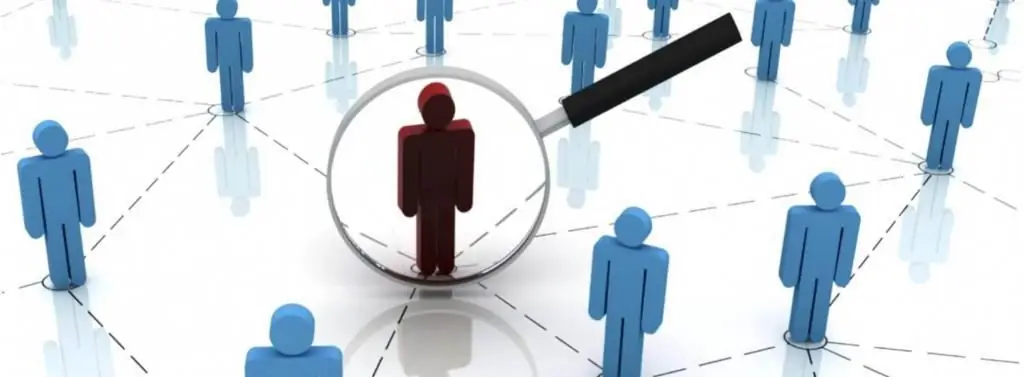
Statybos taisyklės
Vertės srauto atvaizdavimas apima daugybę paprastų veiksmų, kurie greitai sukurs reikiamą projekto modelį su nurodytais parametrais. Pavyzdžiui:
- Atlikite medžiagų ir informacijos srautų analizę, kad gautumėte patikimą vaizdą apie dabartinę proceso būklę.
- Eikite per srautus pirmyn ir atgal, kad nustatytumėte paslėptas nuostolių priežastis ir rastumėte neigiamus modelius.
- Jokiomis aplinkybėmis laiko matavimus atlikite patys, nepasitikėdami kitų specialistų rezultatais ar standartinėmis reikšmėmis.
- Jei įmanoma, sukurkite žemėlapį ir patys, tai leis išvengti tiek svetimų klaidų, tiek šabloninių sprendimų.
- Sutelkite dėmesį į patį gaminį, o ne į operatorių veiksmus ar įrangos dalis.
- Sukurkite žemėlapį rankomis, naudodami pieštuką ar žymeklius.
- Įsivaizduokite proceso elementus naudodami spalvas, kad pagerintumėte suvokimą.
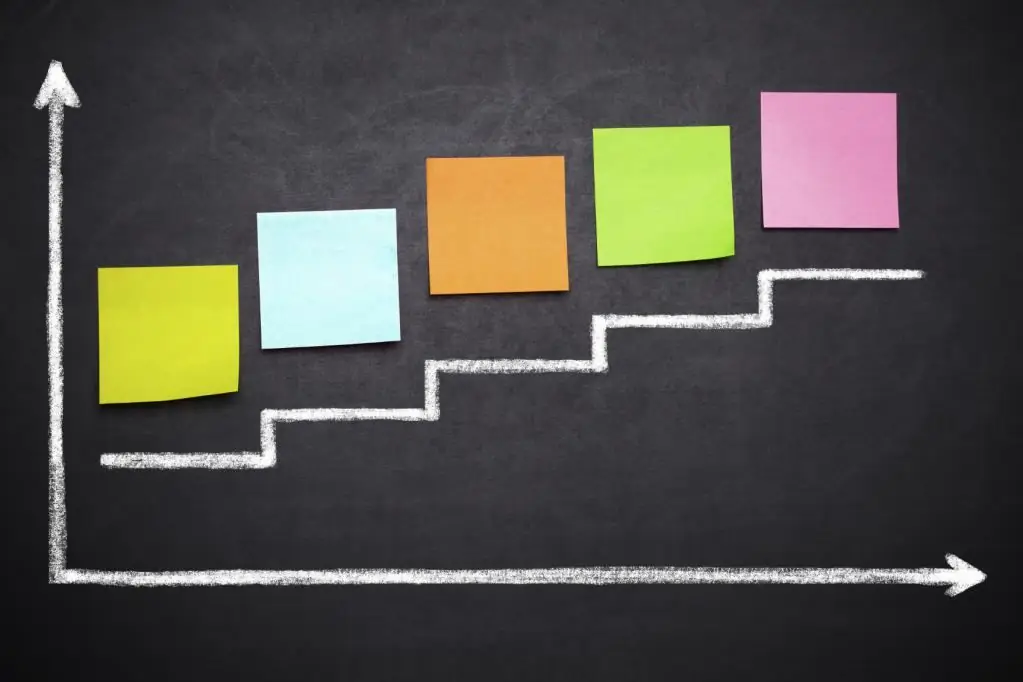
Vertės srauto atvaizdavimo pavyzdžiai
Panagrinėkime srauto žemėlapio sukūrimo pavyzdį dokumentų valdymo srityje, būdingą bet kurios institucijos veiklai.
Pagrindinė užduotis - pasirinkti geriausią tiekėją. Standartinis sprendimo priėmimo procesas yra toks: tiekėjo parinkimas (12 dienų) - sutarties teksto įforminimas (3 dienos) - funkcinių paslaugų derinimas (18 dienų) - įgalioto asmens viza (3 dienos) - gavimas vadovo antspaudas (1 diena) - sandorio šalies parašo gavimas (7 dienos) - registracija institucijose (3 dienos).
Iš viso gauname reikiamą laiką, kad gautume reikiamą sutartį - 48 dienas. Analizės rezultatas - sprendimų priėmimo schemos kliūtys.
Pagrindiniai pakeitimai po žemėlapio analizės:
- Išleistas įsakymas dalį dokumentų pasirašyti padalinių vedėjams (sumažinus administracinio aparato naštą ir gerokai sumažinus derinimų skaičių).
- Visoms paslaugoms sukurti vienodi reikalavimai (bendras supratimas apie reikalavimus sutartiniams dokumentams, sumažėjęs atlikėjų klaidų skaičius).
- Dokumentacijos analizės principas nuo galo iki galo įgyvendintas sudarant bendrą skirtingų tarnybų specialistų grupę.
- Naudoti nauji sutarčių šablonai.
- Optimizuoti dokumentacijos apdorojimo elektroninėje sistemoje mechanizmai.
- Sukurta elektroninė dokumentų kokybės stebėjimo sistema, einanti per proceso etapus.
Pagrindinis rezultatasvertės srauto atvaizdavimas tapo 2 kartus sutrumpėjęs sutartinių dokumentų gavimo laikas, įskaitant patvirtinimo skyrių tarnybose laiką.
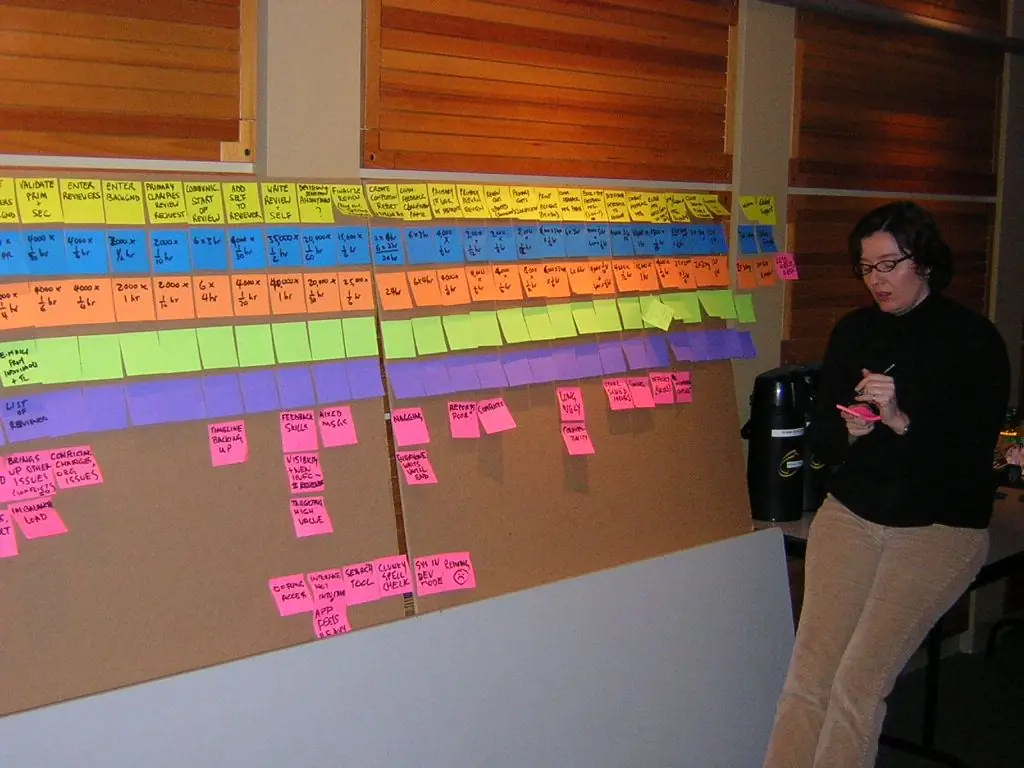
Išvada
Pastaruoju metu vertės srauto žemėlapių sudarymas (VSM, Value Stream Mapping) tapo labai įprastu metodu optimizuojant įvairių organizacijų darbą. Taip yra dėl jo paprastumo ir prieinamumo, minimalių sąnaudų ir teigiamo poveikio, besikaupiančio laikui bėgant. Šios pagrindinės gamybos logistikos metodikos sėkmingo įgyvendinimo pavyzdžių yra daug: „Rostec Corporation“, „Transmashholding“, „Rusijos geležinkeliai“ir kt. Pastaruoju metu medicinos įstaigose federaliniu lygiu buvo sukurta taupios gamybos sistema. Visų pirma, poliklinikose siūloma atlikti vertės srauto kartografavimą.
Kaip matote, visas nagrinėjamo metodo potencialas dar tik pradedamas atskleisti.